How to use cycle stock and safety stock in inventory management
By Jon Taylor on February 19, 2022Inventory is the engine of any company that sells a physical product. But like the engine of a car, without the right fuel, it'll fail to start.
In other words, if a company doesn’t have enough stock to fill its inventory, it faces the dreaded stockout.
To avoid stockouts, most companies rely on strategies like safety stock and cycle stock to optimize inventory levels. The trick is to know what strategies to use and when. This secret sauce not only unlocks lower warehouse and supply chain costs, but it also means customers will always be fulfilled.
This article will look at what cycle stock is, how it differs from other stockout strategies and how to use it to fulfill orders and keep customers happy.
Let’s dive in?
The difference between safety stock vs. cycle stock
We write a lot on our blog about how businesses can safeguard themselves against stockouts. Stockouts are more than just an annoyance for customers; they can become a black hole for company revenue. According to IHL Group research, stockouts cost retailers a whopping $1.2 trillion in 2023, with overstocks totalling $562 billion.
The truth is, a lot of businesses either have too little or too much stock on hand, and this can put huge pressures on cash flow. That’s why so many stock management strategies rely on calculating the right amount of inventory to keep customers happy without overstocking.
While safety stock and cycle stock both play a part in hitting these goals, there are some key differences to be aware of.
What is safety stock?
Safety stock is extra product a company keeps in its warehouse so that every customer order can be fulfilled. It acts as a buffer for unexpected peaks and dips in product sales. It should be used to avoid unexpected changes in customer demand or unpredictable issues with your supply chains.
Think of it as that emergency pizza that’s shoved in your freezer… you know it’s there, but it should really only be busted out if you really need it ?
⚡ Get clued up on all things safety stock
Check out our in-depth guide on how to maximize safety stock levels and combat supply chain uncertainties.
However, this simple formula doesn’t weigh against variables. If a product is seasonal or has a promotional campaign coming up, those factors need to be taken into account. That’s where cycle stock comes into play.
What is cycle stock?
Cycle stock is the inventory expected to be sold based on sales forecasts. It focuses on predicted demand and if your supply chain can cope. In a nutshell, the two are different because:
? Safety stock is the foundational defense for inventory. It’s triggered if stock numbers dip below a specific level.
? Cycle stock avoids stockouts based on calculated demand forecasts that react to fluctuations.
The other main difference between cycle stock and safety stock is how the two figures are calculated.
As safety stock is a static figure that’s triggered when SKU numbers hit a certain level, it traditionally doesn’t really change. On the other hand, cycle stock uses a mix of historical sales data and forecasts to calculate inventory needs, so it can fluctuate.
Let’s take a look at how to make that calculation ?
How to calculate cycle stock
Calculating cycle stock requires two basic inputs: inventory and safety stock.
Cycle stock = Total inventory on hand – safety stock
Let’s say a store sells black headphones. For this SKU, there are 5,000 pairs in inventory, and safety stock levels have been set at 800.
So, the cycle stock needed for the SKU to meet customer demand is 4,200 pairs.
But to get a true reflection of what cycle stock is needed for your inventory, you must also consider economic order quantity (EOQ). This is the number of units needed to minimize inventory and warehouse costs while maximizing product sales.
How to calculate EOQ
To calculate your EOQ, use the following formula:
Economic Order Quantity = √ (2DK / H)
? D represents fixed costs
? K is demand in units
? H is your holding costs
The retailer that stocks the black headphones sells 5,000 pairs a year. But each time they need to replenish stock, the order costs $1500, plus a warehouse fee of $1/unit for storage.
EOQ = √(2* 5000 * $1500 / $1)
Using this formula, the optimal cycle stock to optimize costs is actually 3,873 — nearly 350 units less than the simple calculation we did earlier. This amount of cycle stock will minimize storage and supply chain needs without subjecting the retailer to stockouts.
Cycle stock: why it matters in the real world
According to studies, reducing stockouts and overstocks can cut inventory costs by around 10%.
But limiting stockouts is easier said than done. On paper, it just takes the right inventory calculations. But in the real world, customer demand fluctuates because of everything from the economy to market trends, seasonality, product launches and even competitors.
Even the biggest brands on the planet are not immune to these issues. In 2022, Apple launched its iPhone 14, but there was one huge problem: customers couldn’t get their hands on one!
The problem stemmed from unrest inside a Zhengzhou warehouse, where 200,000 employees made Apple iPhones. After a COVID-19 outbreak inside the factory, some workers fled and walked off the job. As a result, many stores and online retailers had stockouts of the iPhone 14 for Black Friday.
At the time, Reuters reported significantly less stock of the phone than usual.
We believe many Apple Stores now have iPhone 14 Pro shortages based on model or color or storage of up to 25%-30% below normal heading into a typical December, which is not a good sign heading into holiday season.
Reuters
November 2022
Apple shares plummeted 2%, and retailers like Best Buy were forced to warn customers they may not be able to purchase the phone until stocks were replenished.
While this is an extreme example caused by a global pandemic, there are some lessons to learn.
Cycle stock can be used to handle less chaotic demand fluctuations, like a product going viral online or a seasonal spike in sales. While cycle stock isn’t 100% foolproof against every disruption in a supply chain, it can be a significant safeguard if it’s monitored and adjusted to your specific conditions.
To be safe, retailers can use safety stock to help plug the gaps.
If you use the three safety stock strategies listed below alongside the cycle stock calculation from earlier, you will be left with an accurate calculation of what SKU-specific stock must be kept in your inventory:
- Demand safety stock: are your customers going to buy as much as forecasted?
- Supply safety stock: is the supplier going to be on time for their delivery?
- Production safety stock: will we have enough production capacity to produce these goods on time?

How can AI help make better cycle stock decisions?
Most retailers know that calculating the right amount of stock to keep on hand is an agonizing task without the right tools.
These tools are even more important for calculating cycle stock.
As cycle stock fluctuates based on variables like demand, storage costs and suppliers, it relies on accurate data. For a staff member to keep these figures up to date is not only incredibly time consuming, but also opens them up to human error. That’s why adopting artificial intelligence (AI) is the best way for businesses to make cycle stock calculations.
The right tools can track and update data for every SKU in a company’s inventory — data like stock levels, customer demand and supplier costs — to guard against stockouts. Peak’s AI applications can go one step further:
? Abnormal demand response: Our AI for inventory solutions track any daily changes in inventory and supply to search for abnormal demand. If there is a problem with stock levels, Peak can automatically alert the right people to avoid any issues in your supply chain to keep customers happy.
⏱️ Real-time recommendations: Stock levels are tracked in real time. AI replenishment models can make actionable recommendations based on those levels based on customer demand and inventory costs to maximize profits while minimizing stock levels.
? Cycle stock triggers: With Dynamic Inventory, AI can calculate how much cycle stock should be on hand at every distribution center or store. It can also trigger an alert if your cycle stock levels hit a specific point so you know when to reorder to replenish inventory.
Using AI, retailers can optimize every SKU in their inventory while cutting costs. You will still fulfill every customer order and maximize sales.
Talk about a win-win ?
Ready to avoid stockouts forever?
Join our next live demo to see our AI for inventory applications in action.
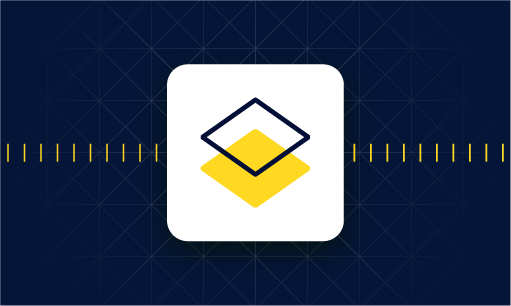
Live demo: see AI for inventory in action
More from Peak
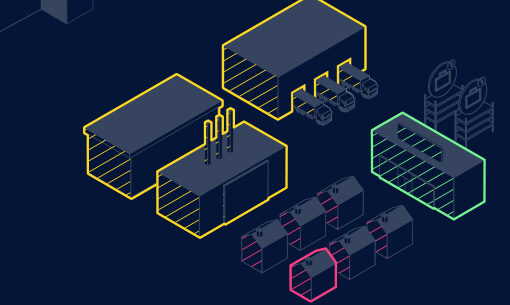
AI for inventory: right stock, right place, right time
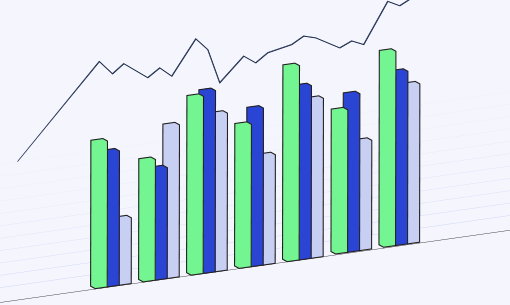