How to calculate safety stock and address supply chain uncertainty
By Josh Tingey and Luke Dyer on August 31, 2023Modern businesses are faced with unprecedented levels of uncertainty.
The volatility we’ve seen in the last few years — COVID-19, war in Ukraine, Brexit, the cost of living crisis and ever-changing consumer expectations, to name a just a few — means that many companies are still waiting on a ‘new normal’ to materialize, with operational disruption and uncertainty commonplace across a number of industries.
What is supply chain uncertainty?
In the world of supply chains, nothing is certain, and decisions often have to be made with imperfect or unknown information. This creates uncertainty, which can come from one of three areas: demand, supply and production.
Demand uncertainty can be triggered by things like forecast accuracy, demand spikes and changing customer behavior.
E.g. Will our customers buy as much as we have forecasted?
Supply uncertainty is often down to late deliveries, partial deliveries or other geopolitical factors.
E.g. Is the supplier going to be on time for their delivery?
Production uncertainty can be caused by issues such as machinery breakages or faults, uncertain yields and employee shortages.
E.g. Will we have enough production capacity to produce these goods on time?
Uncertainty in the supply chain is a problem. It increases the risk of stockouts, missed revenue and poor customer service. However, it’s not all doom and gloom — safety stock can help to address these challenges.
Uncertainty in the supply chain is a problem. It increases the risk of stockouts, missed revenue and poor customer service. Safety stock can help to address these challenges.
What is safety stock?
Safety stock, also often referred to as buffer stock, is an additional inventory of a product strategically kept within a warehouse to proactively avert stockouts.
In the image on the left, we can see that a late delivery from a supplier causes a stockout for several days, as there’s no safety stock to prevent this. On the image on the right, the same late delivery doesn’t lead to a stockout as the additional safety stock provides a buffer.
Safety stock helps to hedge against uncertainty, but it comes at a cost. So, how much safety stock should you hold?
How much safety stock should you hold?
With too little safety stock, there won’t be enough of a buffer to sufficiently cover against uncertainty, leading to more stockouts and more frustrated customers who aren’t able to purchase the products they’re interested in. On the flip side, with too much safety stock your business will be tying up unnecessary capital in stock, as well as paying often extortionate additional storage costs. If your business is dealing with stock that is perishable, this adds a further problem.
In an ideal world, the safety stock level should be ‘just right.’ Finding the optimal balance between still being able to meet service levels and stock holding can help you to maximize monetary KPIs. But finding this level for every SKU across your product portfolio isn’t easy.
Every SKU is affected by uncertainty in a different way. For some, customer demand is easy to forecast whilst for others it may be notoriously difficult to get right. Some suppliers are reliable and always deliver on time whilst others are always late. Some production lines work like clockwork whilst others are always out of action. And, as already mentioned, some stock lasts forever whilst some has a short shelf life.
Finding the right level of safety stock for each SKU
At Peak, we refer to this concept as SKU-specific safety stock. This is made up of three key components:
Demand safety stock. This accounts for the SKU-specific uncertainty associated with demand, e.g. are our customers going to buy as much as forecasted?
Supply safety stock. This accounts for the SKU-specific uncertainty associated with supply, e.g. is this the supplier going to be on time for their delivery?
Production safety stock. This accounts for the SKU-specific uncertainty associated with production, e.g. will we have enough production capacity to produce these goods on time?
These three elements contribute to the total SKU-specific safety stock. This safety stock is not static and changes dynamically as the uncertainty associated with each SKU changes. And, additional forms of uncertainty can also be layered in if required.
Safety stock examples: how is safety stock impacted by real world scenarios?
Scenario one: smooth vs. volatile demand
As we’ve discussed, some customer demand is easy to forecast whilst some is notoriously difficult to get right. In a nutshell, the more uncertain your forecast is, the greater levels of safety stock you need to hold.
Scenario two: late supplier deliveries
Some suppliers are more dependable than others. You’ve worked with them for years, the relationship is strong and you can always rely on them to deliver on time. Others may always be late, or perhaps you’ve only started working with them and can’t yet fully depend on them. The more uncertain your supplier deliveries are the greater the safety stock you need to hold.
Scenario three: production issues
Some production levels always run like clockwork, with straightforward, repeatable processes and little-to-no manual intervention required. Others may have a reputation for being difficult, regularly out of action or require more manual input. The more uncertain your production process is the greater the safety stock you need to hold.
Scenario four: long vs. short lead times
SKUs that have a shorter time between their reorder and delivery dates mean that there is a smaller amount of total uncertainty over a short risk period. This means you can respond to volatility and unexpected events quicker. Items with a longer lead time, meanwhile, will also create a larger uncertainty window. The longer your uncertainty window, the greater the safety stock you need to hold.
This same principle also applies to long and short review periods; the more often you review your stock level position, the less safety stock you need to hold.
Scenario five: low vs. high service levels
As you increase your target service levels for a particular SKU, the amount of safety stock needs to be increased to cover against an increasing number of outlier events.
Different safety stock components scale differently with service level as each is impacted by uncertainty in a distinct way. These five different scenarios all demonstrate how different real-world situations can impact the required levels of safety stock you need to hold for each individual SKU. As you can imagine, when a business holds hundreds or perhaps thousands of SKUs, this can get incredibly complicated.
Let’s dive into a bit more detail and cover Peak’s unique approach to managing safety stock, and some of the key factors you need to be aware of if you’re looking to learn how to calculate safety stock.
How to calculate safety stock: considering volatility
Volatility makes it harder for businesses to forecast accurately, and also leads to erratic peaks and troughs in demand. Both of these aspects should be considered when it comes to calculating safety stock levels, but all too often businesses will look solely at demand volatility.
Forecast volatility
Safety stock exists to cover for unexpected fluctuations in demand. We can calculate the expected size of these fluctuations by looking at our historic forecast errors across the risk periods. This lets us know how well/poorly our forecast has performed historically and therefore how much safety stock we should hold for each SKU.
Why not just look at demand volatility?
We only want to hold safety stock for unexpected volatility in demand. If we know there’s a large order in four weeks time then it is forecastable and so we don’t need to hold safety stock to account for it.
How to calculate safety stock: setting a safety stock level
Forecast error distribution
By looking at the size and frequency of the forecast errors we can create a forecast error distribution. Lots of businesses assume a normal distribution, but we know that isn’t appropriate in practice. At Peak we use a non-parametric method for calculating the distribution, to ensure that the tails of the distribution are considered properly.
Service level choice
This forecast error distribution can then be converted into percentiles. From this we can choose a percentile and find the corresponding safety stock value. This percentile represents that when a forecast error occurs, 98.5% of the time it will be smaller than the equivalent value.
How to calculate safety stock: the standard approach
Order placing
The standard approach Peak uses for inventory optimization involves placing a single large order to cover the current difference to the reorder point (ROP), plus the forecasted demand over the next risk period (review period plus lead time).
Impact
Because you’re placing a larger order instead of lots of little ones, it means cheaper delivery costs, less orders to place and longer production cycles. However it does mean you would hold more safety stock on average.
How to calculate safety stock: the ‘little and often’ approach
Order placing
The little and often approach involves placing smaller, more regular orders to just cover the current difference to the ROP, plus the forecasted demand over the next review period (instead of the entire risk period).
Impact
Because of these more regular, smaller orders it means the average inventory position is significantly lower. Whilst this loses some of the “standard” approach benefits. It instead allows you to hold a lower average inventory alongside reducing the likelihood of stock expiring.
How to calculate safety stock: Peak’s approach in summary
We use safety stock to hedge against volatility in demand. We estimate the distribution of forecast errors, and the safety stock level is chosen based on the desired service level within that distribution.
We can also consider additional forms of uncertainty e.g. the lead times of your suppliers. And, crucially, thanks to our Dynamic Inventory application, we can understand the cost trade-off and pick an appropriate service level.
Hopefully this guide has given you more insight into safety stock, and the approach we take at Peak to deal with volatility. Inventory levels can make or break a business, so if you want to learn more about the steps you can take to get a smarter view of your stock, you can book a demo to see our Dynamic Inventory application in action via the button below.
Discover Dynamic Inventory and optimize your safety stock levels
Maximize margins, while avoiding stockouts, wastage and unnecessary costs. Check out our Dynamic Inventory application to learn more.
Check out some related downloadable content
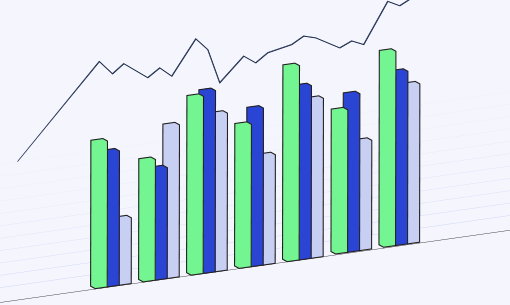
Demand forecasting: the leap to advanced machine learning
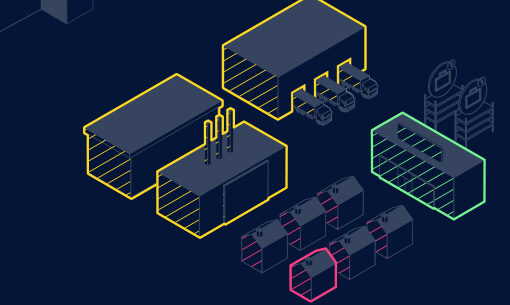
AI for inventory: right stock, right place, right time
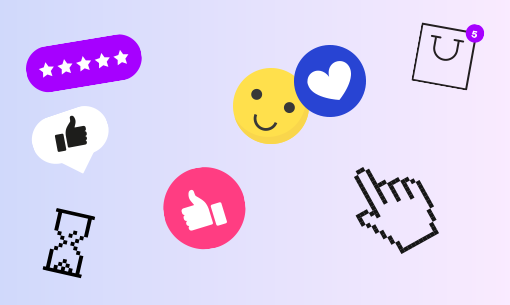